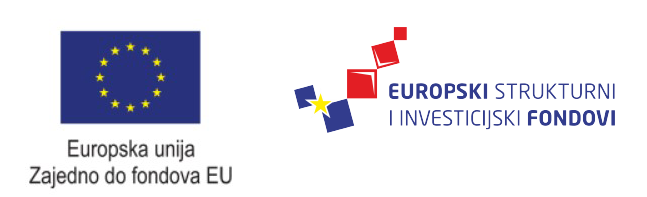
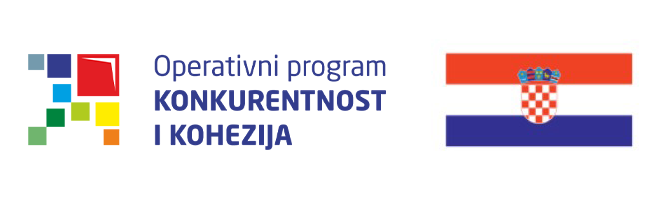
21.10.2019. – Company has recently added new soldering equipment to its PCB assembly technology portfolio. By purchasing latest vapor phase reflux machine, we can now reliably solder PCBs with parts with different masses, which usually which makes the soldering process complicated.
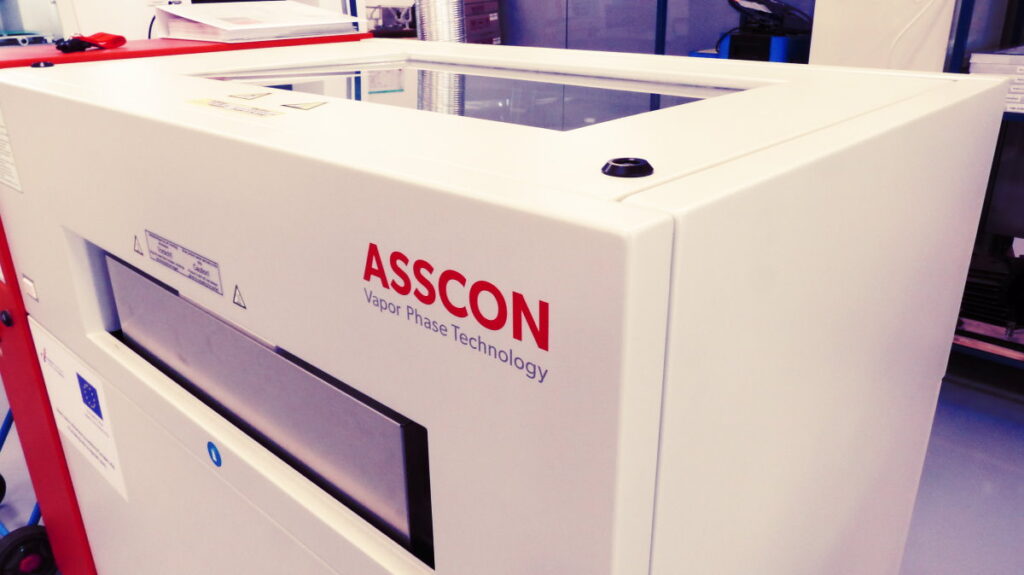
Excellent temperature control
Most significant benefits of vapor phase reflow is that it enables excellent temperature control. At atmospheric pressure, the vapor’s temperature is the same as the temperature of the boiling liquid which means there are minimal temperature fluctuations during soldering process. Opposite to the convection or infrared heating methods, in case you increase the temperature, the rate of vapor production will also increase, but there’ll be no change in the temperature. Vapor and soldering temperature are defined only by the vapor type used.
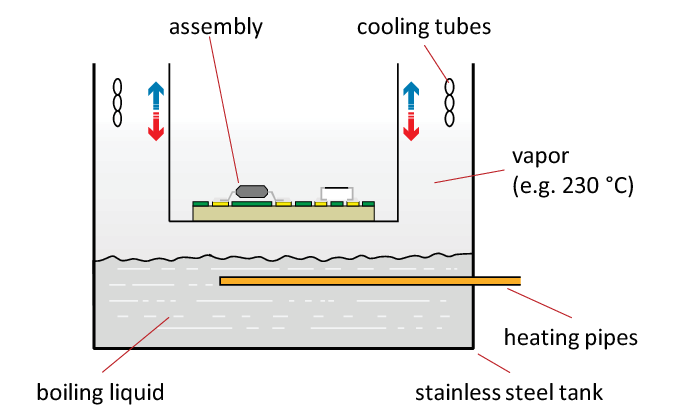
Uniform heating
Factors like size, shape, color, or geometric of PCB components do not affect the vapor phase reflow process, which exposes each part of each element to precisely the same temperature. It makes the vapor phase reflow process perfect for reflowing multilayer boards and large boards. VPR is also ideal for panels with variously sized pieces and boards with a dense population.
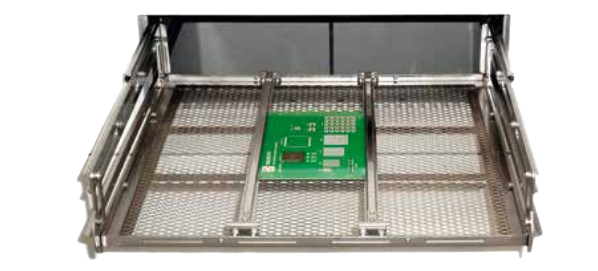
Higher heat transfer rate
The vapor phase reflow process requires lower temperature for ensuring an ideal soldering spot. Most reflow methods need up to 35°C extra heat for perfect soldering, where vapor phase needs only 5 to 10°C over the solder paste’s melting point for perfect soldering spot.
Excellent wettability
The vapor phase reflow process offers oxygen-free soldering atmosphere. For this reason, you get superior wetting at no additional cost. There’s much lower energy consumption than in the convectional oven reflow process, and there is a minimal release of heat into the surrounding environment, which means no additional air conditioning is required.
More environmentally friendly
The vapor phase reflow process is also one of the cleanest and safest. Vapor phase soldering machine does not need volatile organic compounds to operate. Fluorinated fluids are inert, nontoxic, noncorrosive, nonflammable, and nonpolluting. These fluids usually evaporate entirely from the board and leave no residue behind, which makes vapor phase one of the most eco-friendly reflow processes around.
Implementation of the project is co-financed from the European Structural and Investment Funds in the financial period 2014-2020.
More information
Content of this publication is exclusive responsibility of Dilogic d.o.o.
Latest News
Dilogic moved to new building
03.07.2019.