Überblick
Unser langjähriger Partner TDK-Croatia ist ein Hersteller von elektronischen Bauteilen. Um die Ausbeute bei der Herstellung von Varistoren zu verbessern, war es notwendig, eine präzise Messung der verwendeten Rohkomponenten einzuführen. Da die Messung in die Produktionslinie integriert werden sollte, musste sie vollautomatisch, schnell, präzise und äußerst zuverlässig sein.
Die im Varistor-Herstellungsprozess verwendeten Rohkomponenten sind recht klein (im Sub-Millimeter-Bereich). Neben den grundlegenden Abmessungen mussten auch die Krümmungsradien an den Kanten und den beiden Diagonalen des Bauteils gemessen werden.
Der gesamte Prozessablauf besteht darin, eine repräsentative statistische Stichprobe von einigen Dutzend Bauteilen aus jeder Charge zu messen und dann auf der Grundlage der ermittelten Ergebnisse die Produktionsparameter der weiteren technologischen Prozesse festzulegen. Die gesammelten Ergebnisse werden auch automatisch im internen Qualitätskontrollsystem gespeichert.
Lösung
Aufgrund der geringen Größe der Bauteile musste die Messung mit einem Mikroskop in Verbindung mit einer kalibrierten Kamera durchgeführt werden. Die gesammelten Bilder wurden dann mit Hilfe von Computer Vision verarbeitet. Ein intelligenter Algorithmus wurde entwickelt, um das Probenbild zu analysieren, so dass alle erforderlichen Parameter in einem einzigen Schritt präzise und schnell gemessen werden konnten. Für jedes Bauteil mussten die Ergebnisse auch automatisch überprüft werden, um die Plausibilität der erfassten Parameter sicherzustellen.
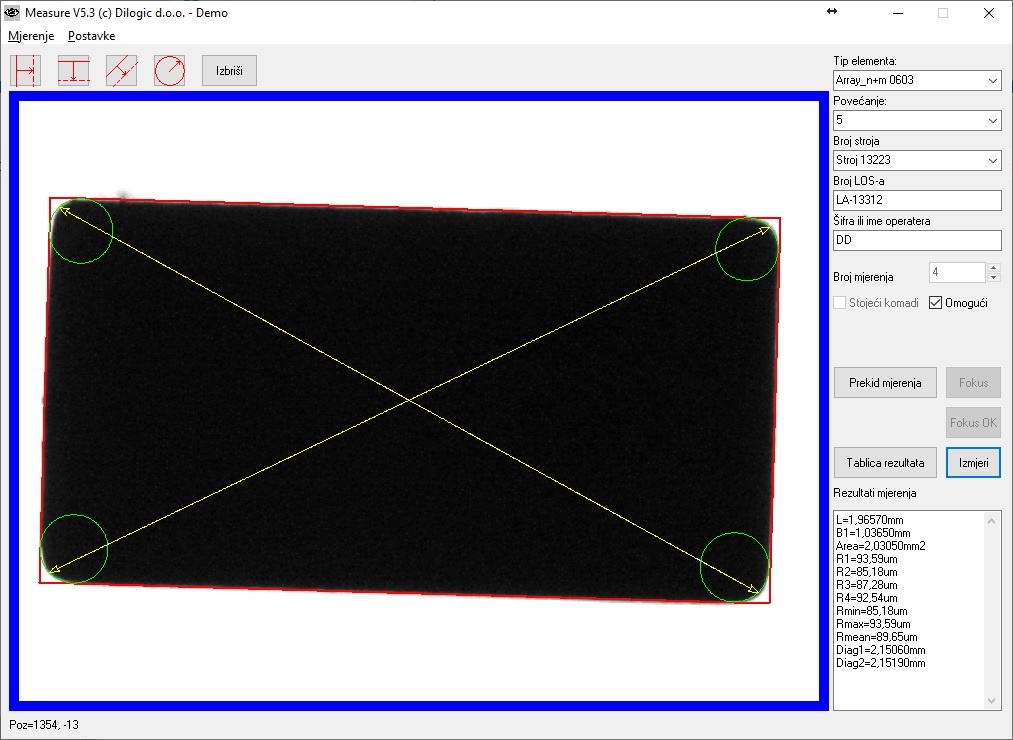
Neben den ermittelten Abmessungen ist ein weiterer wichtiger Parameter, in diesem Prozess, das durchschnittliche Gewicht der Bauteile, das ebenfalls genau bestimmt werden musste. Da die Masse der einzelnen Komponenten sehr gering ist, bestand die Lösung darin, so viele Komponenten wie möglich zu messen, um dann mit der Anzahl der gemessenen Komponenten die genaue Durchschnittsmaße jeder Komponente zu berechnen.
Zum Zählen und Wiegen der Komponenten wird ein spezielles geeichtes Sieb (eine Maske mit Öffnungen) verwendet, dessen Öffnungen groß genug sind, um nur eine Komponente aufzunehmen. Das Sieb ist groß genug, um mehrere Tausend Komponenten aufzunehmen. Das Problem, das bei diesem Verfahren zu lösen war, bestand darin, dass nach dem Auflegen der Komponenten auf die Maske nicht alle Öffnungen mit Komponenten gefüllt waren, so dass die Anzahl der fehlenden Komponenten genau gezählt werden musste.
Auch hier bestand die Lösung darin, ein hochauflösendes Bild der Maske mit Bauteilen aufzunehmen und durch digitale Verarbeitung des Bildes festzustellen, wie viele Bauteile in der Maske fehlen.
Die Ingenieure von Dilogic konstruierten und produzierten ein spezielles Gerät mit Kamera und Beleuchtung, mit dem das Bild der Maske aufgenommen wurde. Ein spezieller Computer-Vision-Algorithmus wurde entwickelt, um die fehlenden Komponenten genau zu erkennen und ihre Anzahl zu zählen. Da die Anzahl der Öffnungen in der Maske sowie das Gewicht der leeren Maske bekannt sind, kann durch Wiegen der vollen Maske und der Anzahl der fehlenden Komponenten das durchschnittliche Gewicht jeder einzelnen Komponente berechnet werden.
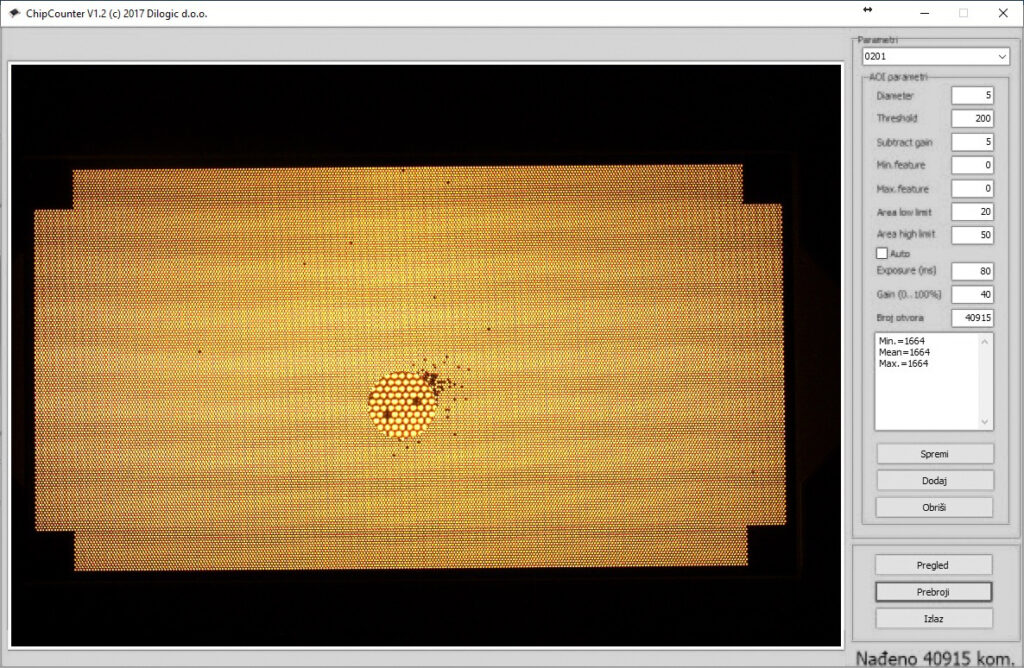