Overview
Our long-term partner TDK-Croatia is manufacturer of electronic components. In order to improve yield of varistor manufacturing process, there was a need to introduce precise measurement of raw components used. Measurement was to be included in production line, so it needed to be fully automated, fast, precise and extremely reliable.
Raw component used in varistor production process is quite small (sub-milimeter size). Along basic dimensions, there was a need to measure radius of curvature on component edges and both diagonals of component.
The complete process workflow is to measure representative statistical sample of few dozens of components from each batch, and then, on the base of averaged results production parameters of further technological processes are set. Gathered results are also automatically stored into internal quality control system.
Solution
Due to small size of components, measurement needed to be done using a microscope coupled to a calibrated camera. Gathered images were then processed using computer vision. Smart algorithm was developed to analyze the sample image so all required parameters could be precisely and quickly measured in single step. For each component results also had to be automatically verified to ensure plausibility of gathered parameters.
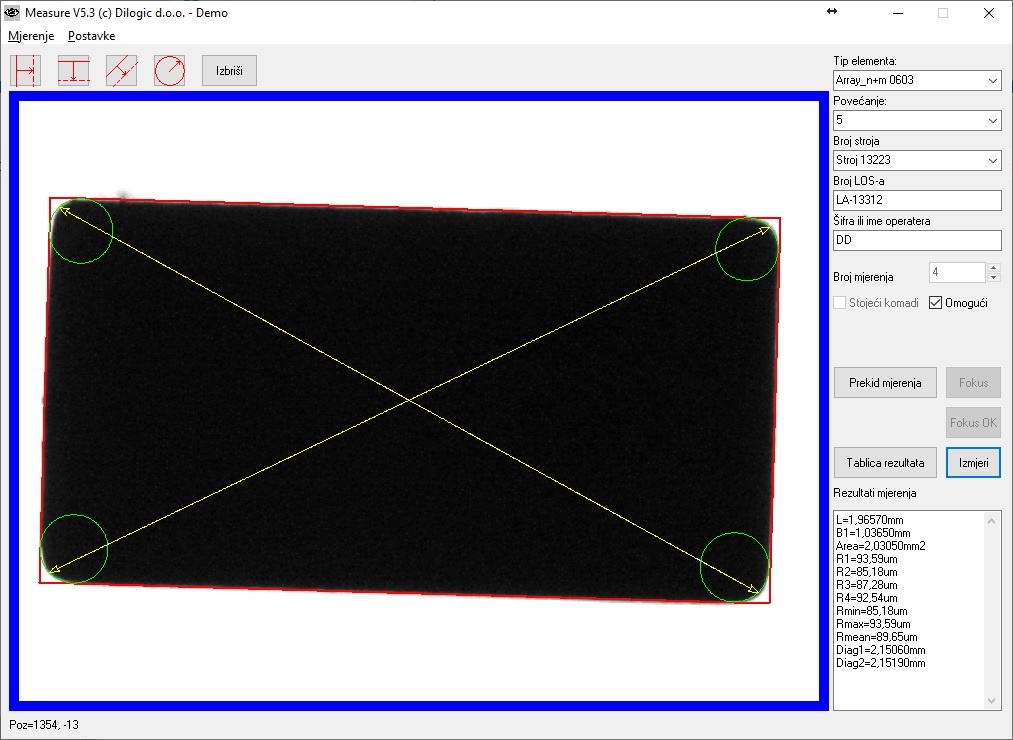
Along with measured dimensions, another important parameter in the process is the average weight of component which also had to be determined precisely. Due to very small mass of each component, solution was to measure as many components as possible, and then, by knowing number of components measured precise average mass of each component could be calculated.
To count and weigh batch of components, special calibrated sieve (a mask with openings) is used, with openings large enough to accommodate just one component. The sieve is large enough to accommodate several thousands of components. The problem to solve in the process was that, after components are placed on the mask, not all openings were filled with components, so number of missing components had to be precisely counted.
Again, the solution was to capture high resolution image of the mask with components, and by digitally processing the image detect how many components in the mask are missing.
Engineers from Dilogic constructed and produces special apparatus with camera and illumination which is used to take the image of the mask. Special computer vision algorithm was developed to precisely detect missing components and count their number. As number of openings in the mask is known, as well as the weight of the empty mask, by weighing full mask and number of missing components average weight of each single component can be calculated.
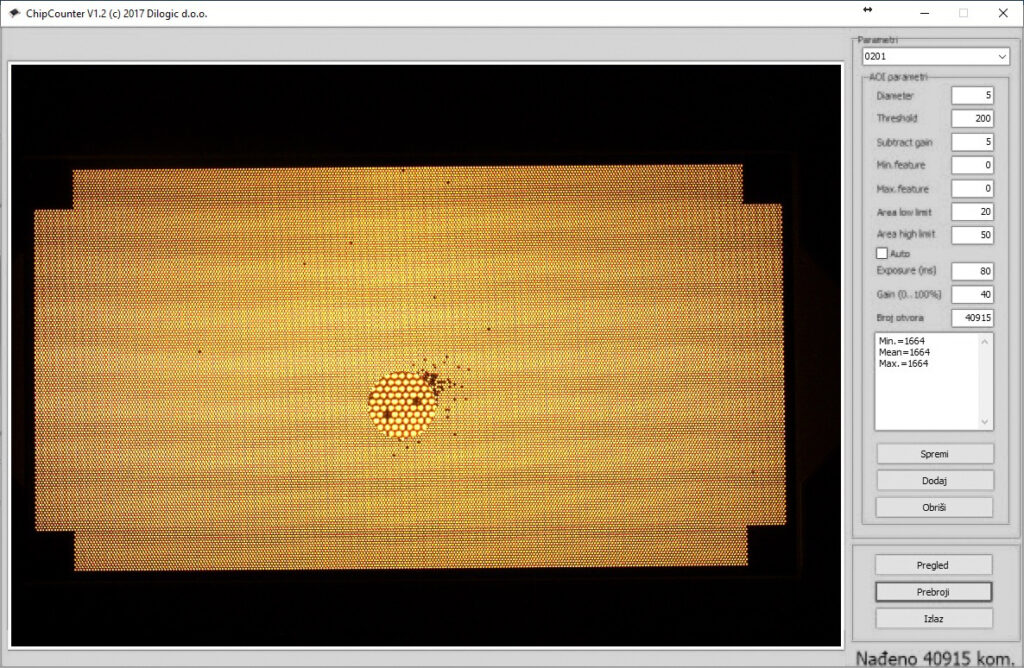